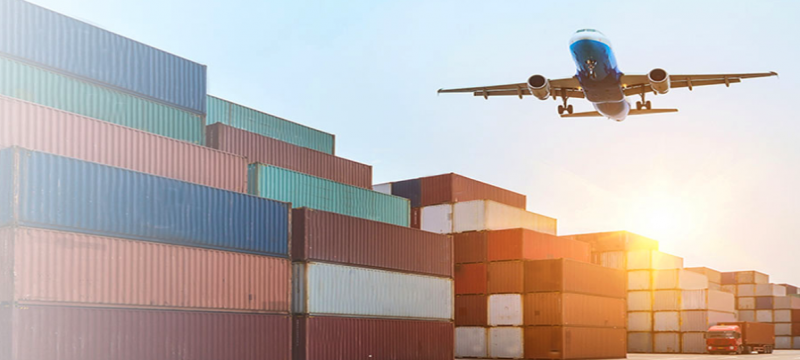
What actually is Cross Docking?
What is Cross Docking - understanding the concept and definition?
The speed and productivity of the supply chain has become an important growth factor for organizations. Cross-docking is just one strategy that can be implemented to help achieve a competitive advantage. Applied appropriately and under the right conditions, cross-docking can provide significant improvements in efficiency and operating time. As a definition of cross docking, we can say that “cross docking is a logistical strategy where the carrier immediately unloads the cargo from an incoming container and then loads it directly to an outgoing carrier. This is a practice that keeps supply chains moving in a productive and efficient way. ”
What is Cross Docking?
Cross-docking is a logistical procedure in which products from a supplier or production plant are distributed directly to a customer or retail chain - without time for processing or storage. Cross-docking takes place at a docking terminal for distribution; it usually consists of trucks and dock doors on two (entry and exit) sides with minimal storage space. The name "cross docking" explains the process of receiving products through an incoming dock and then transferring them through the dock to the outgoing transport dock.
Simply put, incoming products arrive by transport such as trucks / trailers and are distributed to a receiving dock. Once inbound transport is attached, its products can be moved directly or indirectly to outbound destinations; they can be unloaded, sorted and screened to identify their final destinations. Once sorted, the products are moved to the other end of the terminal by forklift, conveyor, pallet truck or other vehicle to their intended exit dock. When the outbound transport is busy, the products can make their way to the customers.
How exactly does Cross Docking work?
In essence, cross-docking removes the link 'storage' of goods in the supply chain. The products are unloaded from a truck or truck, sorted and reloaded directly into outgoing trucks or rail cars to continue their journey. Products that go to the same destination can easily be consolidated into fewer vehicles. Alternatively, large shipments can also be broken down into smaller groups for easier delivery. The end result in both scenarios is a stricter, more efficient supply chain. It is advisable to avoid storing products. Therefore: Every time a product is stored, it is a time when it does not generate income for the company or the customer. In addition, storage time introduces additional risk.
Here are some key reasons why a company should avoid storing products:
- Decrease in value - Prices of products stored in stock can potentially fall due to changes in demand, expiration issues and more.
- Change in demand - Demand for most products changes over time and in many cases declines. Products in stock are at risk of becoming unwanted and therefore cost less.
- Damage or theft - Having products on a shelf in a warehouse puts them at risk of damage, theft or other problems.
When is cross docking used?
The cross-docking process will not meet the needs of every warehouse, so it is important to make an informed decision about whether cross-docking will increase productivity, costs and customer satisfaction for your particular business. This method can improve the supply chain for various specific products. For a canned or temperature-controlled item, such as food that needs to be transported as quickly as possible, this process can benefit.
Three of the main types of cross docking are to:
- Provide a central location for products that will be sorted and combined with similar products to be delivered to multiple destinations by the most productive and fastest method.
- Combine many smaller loads of products in one transport method to save on transportation costs.
- Break large loads of products into smaller loads to transport to create an easier delivery process to the customer.
What are the benefits of Cross Docking?
Transportation companies love this transportation practice because trucks have fuller loads and more accurate destinations for each shipment, which saves on shipping costs. In this way, the sender can quickly adapt to new sales channels and market conditions; this delivery method reduces the total time to reach each customer. Although this practice provides significant financial and operational benefits, in order to achieve effective results, companies must implement proper monitoring and compliance. Like other supply chain practices, cross-docking requires control and visibility of the shipment from the supplier to the end customer.
Advantages of Cross Docking
Although it is certainly not the right logistics strategy for every company, it can provide very great benefits when used properly. Some key benefits include:
- Control - Companies have the ability to target product levels at a much more detailed level. This ensures that each store receives exactly what is needed to meet customer needs, no more and no less.
- Just in time - cross docking is often used for timely production, where supplies are delivered where they are needed, as they are needed to ensure that there is no unnecessary storage of parts or products.
- Lower warehousing costs - With this type of distribution strategy, there is much less need for warehousing products, which saves companies money.
- Organization - When applied correctly, this strategy can help the company have a more organized supply line.
- Reduced labor costs - With less storage and warehousing, there is less need for people to handle the products, which can help reduce labor costs.
In conclusion, we will tell you which are the most suitable products for cross docking. There are materials that are more suitable for cross docking than others. The list below shows a number of types of materials that are more suitable for cross docking.
- Perishable items that require immediate delivery
- High quality items that do not require quality checks upon receipt of goods
- Products that are pre-marked (barcodes, RFID), pre-placed tickets and ready for sale
- Promotional items and items that are now on the market
- Basic retail products with a deviation in constant demand or low demand
- Pre-selected, pre-packaged customer orders from another production plant or warehouse